- November 2, 2024
- Posted by: DM Airon Academy
- Categories:
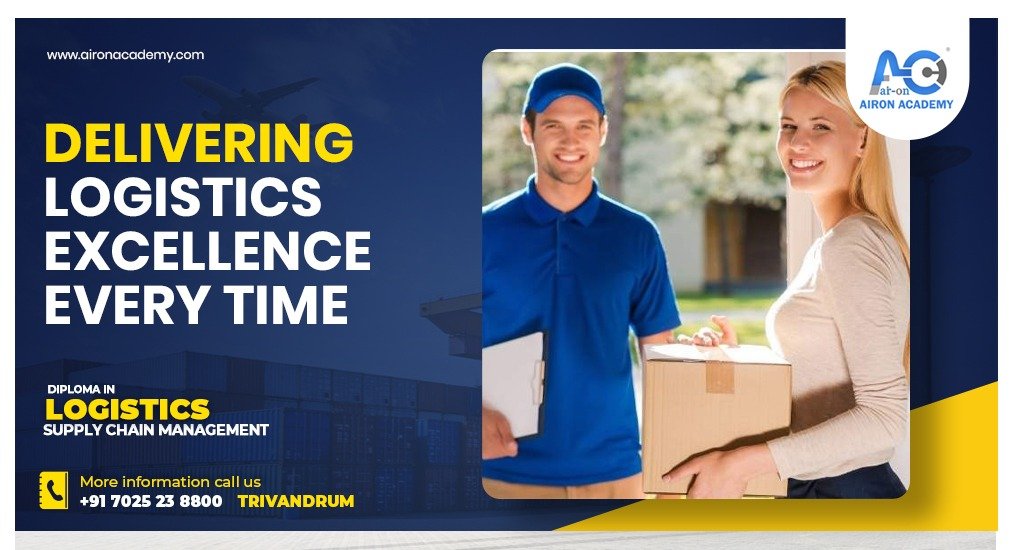
Supply chain and logistics organizations are facing the hard reality of needing to stay productive and profitable amid the ongoing labor shortage. A recent Descartes survey of supply chain and logistics leaders across North America and Europe found that 76% of respondents are experiencing notable workforce shortages in their operations, with 37% characterizing the shortage as high to extreme—a serious obstacle to growth.
While the impact of the labor shortage can be felt across the entire organization — from demand planning and customer service to distribution planning and transportation planning — the survey revealed that transportation operations (61%) and warehouse operations (56%) are suffering the most from the lack of workers.
In addition to being unable to meet the resource requirements of labor-intensive functions in the warehouse and transportation domains, the survey observed that supply chain and logistics organizations are finding open positions for knowledge workers (such as planners and analysts) the hardest positions to fill (55% hard to extremely hard), followed closely by managers (54%). This shortfall will become even more problematic as supply chain and logistics operations become increasingly data-driven and technology-enabled.
A Widespread Impact
In addition to the underlying global demographics of 50 years of birth rates below replacement levels, multiple factors are compounding the ongoing talent shortage: the growing wave of Baby Boomer retirements, several years of falling immigration numbers, and a decline in labor force participation. The fallout from the lack of workers in the workforce is widespread, causing logistical and performance headaches for logistics and supply chain organizations.
The effects of the labor shortage are impacting business processes in the front office, on the warehouse floor, and across distribution operations, creating a ripple effect that compromises growth. With financial performance dependent upon stable operations, including a workforce with accumulated deep domain expertise, the labor shortage is taking a bite out of profits.
Plus, in an employees’ market, workers have the freedom to seek greener employment pastures, creating turnover issues — and an uphill battle to protect margins — for supply chain organizations.
With the pressure peak season places on the hiring process and scaling operations to meet increased demand, it’s no surprise that almost half of survey respondents said performance during peak season is “very to extremely” impacted by the labor shortage. Given the resource-intensive nature of supply chain and logistics operations, 58% of survey respondents indicated that the worker shortage is taking a toll on customer service.
Additionally, because supply chain and logistics operations involve multi-party processes, many organizations rely heavily on logistics partners to execute resource-intensive warehouse and transportation operations. A mere 9% of survey respondents indicated that their logistics partners’ performance was not impacted by the workforce shortage.
First Line of Defense
To offset the impact of fewer available laborers, knowledge workers, and managers, many supply chain organizations have turned to technology and automation to increase productivity. In fact, the 2024 Descartes study found that the top organizational strategy overall to improve worker productivity is automating non-value-added and repetitive tasks (54% of respondents) using technologies such as warehouse management, driver mobile productivity, and delivery route optimization. By alleviating the burden of the many routine, non-integrated supply chain and logistics functions that require manual intervention, companies can accomplish more with fewer workers.
In addition to increasing the efficiency of labor roles, automated technology tools are being deployed to boost the productivity of knowledge workers, reducing the time spent preparing data and running reports and freeing up time to conduct higher-value analysis and planning.
Given the highly manual and resource-intensive nature of shipment tracking, it’s no surprise that real-time shipment tracking was the most commonly cited partially or fully deployed technology (53% of respondents) used to address the knowledge worker shortage. Back-office automation (47%), advanced analytics (47%) and digital customer self-service (43%) also proved to be popular automation strategies for mitigating the impact of the labor shortage.
In addition, supply chain and logistics organizations are opting to co-mingle operations with other divisions (50% of respondents) and centralize operations (50%) to reduce the dependency on hiring workers, a critical factor during peak season.
The People Management Front
Companies have been forced to adapt their recruitment and retention strategies to optimize their workforce. Notably, the Descartes study found that organizations most altered their strategies for hiring laborers and knowledge workers (54% of respondents).
Logistics-oriented companies have changed their approach to hiring new talent, offering multiple perks and benefits to attract candidates, such as working time flexibility (35% “significantly used” this tactic) and adopting the latest technology (34%). Both approaches particularly appeal to Millennials and Gen Z demographics. And, when it comes to offering higher pay to attract new hires, 31% of respondents noted they significantly used this specific tactic.
To address the shortfall, supply chain and logistics organizations are also turning to educational and governmental organizations, such as trade schools and universities, to attract both labor and knowledge workers. Similarly, they are filling labor gaps with alternative workforce sources, including immigrants (37% of respondents), people with disabilities (34%), and those formerly incarcerated or from social rehabilitation programs (30%). Notably, the use of immigrants by financially industry-leading respondents is significantly higher (54%) compared to financially below-average organizations (27%).
The Retention Factor
With the labor shortage likely to persist indefinitely, companies must prioritize a strategy to not only attract talent but also to retain the workers they have. The Descartes study found that the 74% of respondents experiencing above-average to industry-leading financial performance reported better-than-average employee turnover, dropping to 24% for those with worse-than-average turnover.
On the flip side, the percentage of supply chain leaders with “slightly to significantly better-than-average” employee turnover jumped from 41% overall to 68% for those with industry-leading financial performance, and dropped to 18% for those with below-average financial performance — demonstrating the link between being an employer of choice and higher-performing supply chain and logistics operations.
Supply chain and logistics organizations are employing a range of employee-focused tactics. The Descartes survey found that providing on-the-job training and education compensation was the most significantly used tactic (35%) for retaining workers, followed closely by offering higher pay (34%).
Companies are working hard to keep their current employees happy, offering a range of benefits including working time flexibility, career planning and promotion programs, team-building activities, retention bonuses/rewards programs, and work-from-home options, among others.
When demand for employees outstrips supply, workers have the upper hand, with the option to change companies, or even industries, to find a more rewarding job experience. To become employers of choice, savvy supply chain and logistics leaders are looking to create a sticky workplace culture that helps mitigate the impact of the labor shortage in the following ways:
- Making employees’ roles more productive with automation and AI. Supply chain and logistics organizations are simplifying, streamlining, and accelerating workflows and business processes to eliminate lower-value, repetitive tasks for both laborers and knowledge workers. Automated technology such as barcode-based picking, and tools such as route-optimization and freight-visibility platforms, are the top choices.
- Spotlighting leading technology. Employees today, especially Millennials and Gen Z, want to work for companies that deploy modern technology. Logistics and supply chain companies must ensure their tech stack includes leading technology that not only simplifies workers’ daily tasks, but helps them grow in their roles.
- Not overlooking hourly workers. Supply chain leaders must take steps to enhance employee experience through on-the-job skills enrichment, career development, mentorship, and good communication and feedback.
While many forward-thinking companies are turning to innovative technology, rethinking employee acquisition and retention strategies is equally important. The combined approach of automating labor-intensive tasks, in tandem with adapting people-management strategies to optimize hiring and retention, helps differentiate supply chain and logistics organizations from the competition.