- November 19, 2024
- Posted by: DM Airon Academy
- Categories:
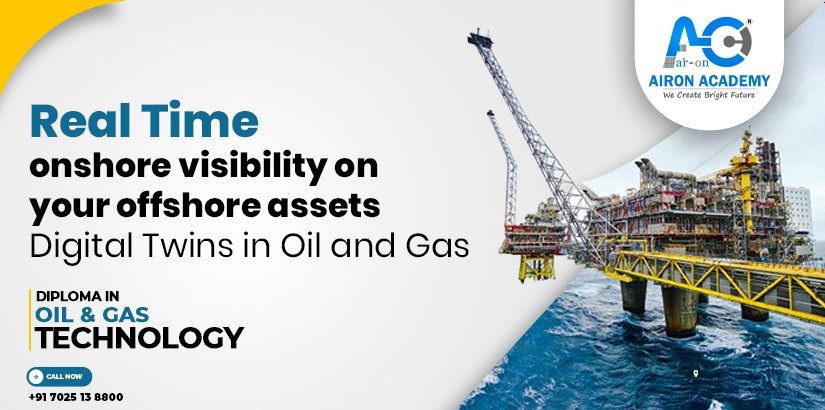
The oil and gas industry faces unique challenges in managing offshore assets, such as platforms, rigs, and subsea infrastructure. Digital twin technology has emerged as a powerful solution to bridge the gap between onshore operations and offshore environments by offering real-time visibility and actionable insights. Here’s how:
What Are Digital Twins?
A digital twin is a virtual replica of a physical asset, system, or process. It combines real-time data, simulations, and analytics to create a dynamic digital representation of an asset. For offshore oil and gas, digital twins integrate data from sensors, IoT devices, and advanced modeling tools to monitor operations remotely.
Key Benefits of Digital Twins in Oil and Gas
- Real-Time Monitoring and Analysis:
- Digital twins enable continuous monitoring of offshore assets.
- Real-time data from equipment like pumps, pipelines, and drilling rigs is transmitted to onshore control centers for analysis.
- Operators can detect anomalies early, such as equipment malfunctions or leaks.
- Predictive Maintenance:
- Using AI and machine learning, digital twins can predict when critical components might fail.
- This reduces downtime, avoids costly repairs, and improves asset lifespan.
- Operational Optimization:
- Simulations run on the digital twin allow for scenario testing, such as adjusting drilling parameters or optimizing production rates.
- These insights help in reducing energy consumption and improving efficiency.
- Enhanced Safety and Risk Management:
- Digital twins help identify potential risks, such as pressure buildup or structural weaknesses, before they become critical.
- Emergency scenarios can be simulated to improve response strategies.
- Remote Collaboration:
- Teams onshore and offshore can collaborate using real-time digital representations.
- This minimizes the need for on-site personnel, reducing costs and enhancing safety.
Key Components in Digital Twin Implementation
- Data Collection: IoT sensors and edge devices installed on offshore assets provide continuous streams of data.
- Integration Platforms: Cloud-based systems consolidate data and allow seamless access to stakeholders.
- Advanced Analytics: AI-driven tools analyze patterns and provide actionable insights.
- Visualization Tools: 3D models and virtual environments enable intuitive exploration of asset performance.
Case Studies and Applications
- Subsea Infrastructure: Monitoring pipeline integrity and flow rates to ensure uninterrupted transport of hydrocarbons.
- Drilling Operations: Optimizing drilling parameters in real-time to increase efficiency and reduce costs.
- FPSOs (Floating Production, Storage, and Offloading): Managing complex systems to prevent downtime and improve productivity.
Challenges and Future Prospects
- Data Integration: Bringing together diverse data sources into a cohesive digital twin requires robust infrastructure.
- Cybersecurity: Protecting sensitive operational data is critical.
- Scalability: Expanding digital twin applications to larger and more complex systems.
Digital twins are revolutionizing the oil and gas industry by providing unparalleled visibility, efficiency, and safety for offshore operations. As technology advances, their role in creating a connected and optimized energy ecosystem will only grow.
Industry growth and innovation
Late in 2018 we reported that a recent oil and gas customers in this sector had implemented IFS software onshore and offshore across seven rigs in only six months. The need for a rapid implementation was a priority for Borr Drilling and was one of the main reasons for investing in IFS Applications.
Borr Drilling found the solution a perfect fit for its business, with robust, industry-specific functionality for offshore drilling contractors. The IFS solution deployed supports mission-critical business processes including enterprise asset management (EAM), onshore-offshore data replication, supply chain management, financials, and document management.
But within this very tough sector, the pressure is on to utilize digital innovation in order to lead or challenge. However, it is important to ensure an innovation is not a single point initiative that delivers a proof of concept. Rather innovation is a top-down program of change for the organization focused on the process areas that have the potential to unlock the greatest value.
One way in which digital innovation can be driven into a business is through linking to an Asset Performance Management (APM) focus. According to Jonathan Leow, Senior Research Manager at IDC, the aim of APM is to enhance operating efficiency and reduce operating costs through increased asset uptime and availability. This further suggests that operational efficiency and reduced operating costs can be achieved through plant simulations integrating operational data with enterprise data. Something that is best done by creating a digital twin that can represent the assets and connect with the strategic vision of the company.
Digital Twin
A digital twin is a software-based replica of business assets, processes, and systems which are based on the Internet of Things (IoT).
- A Digital Twin can be used as a key for successful business transformations.
- As a digital representation, a Digital Twin provides both the elements and the dynamics of how an Industrial Internet of Things (IIoT) device operates throughout its lifecycle. Using this technology, an organization can increase predictability and lower risks.
- A Digital Twin is an up-to-date and accurate copy of the physical object’s properties and states, including their position, shape, status and motion.
For companies in oil and gas, a digital twin could provide onshore head office with real-time as-is visibility of each individual rig’s condition and performance across the end-to-end process – with the potential for connected Internet of Things sensors and on-rig asset management data combining.
This allows senior leaders at oil and gascompanies to achieve a real ‘as-designed,’ ‘as-built,’ ‘as-operated’ visibility into their fleet of globally distributed assets, enabling them to quickly and efficiently re-plan and reposition the fleet to access new opportunities globally.
The Operational Intelligence solution from IFS allows companies to create a Digital Twin of the organization, which will help in focusing decision making in respect of asset performance management.
Creating a Digital Twins of the Organization (DTO) is provides visibility of data that otherwise would exist in silos within the business. The operational intelligence solution from IFS provides an integrated view of all business areas, processes and key performance, risks, compliance and financial results. Reporting quality and time-to-action improves significantly because IFS Enterprise Operational Intelligence provides model-driven predictive analysis capabilities that combine data mining algorithmic models and forward-looking what-if scenario planning.